Concept Sketch:
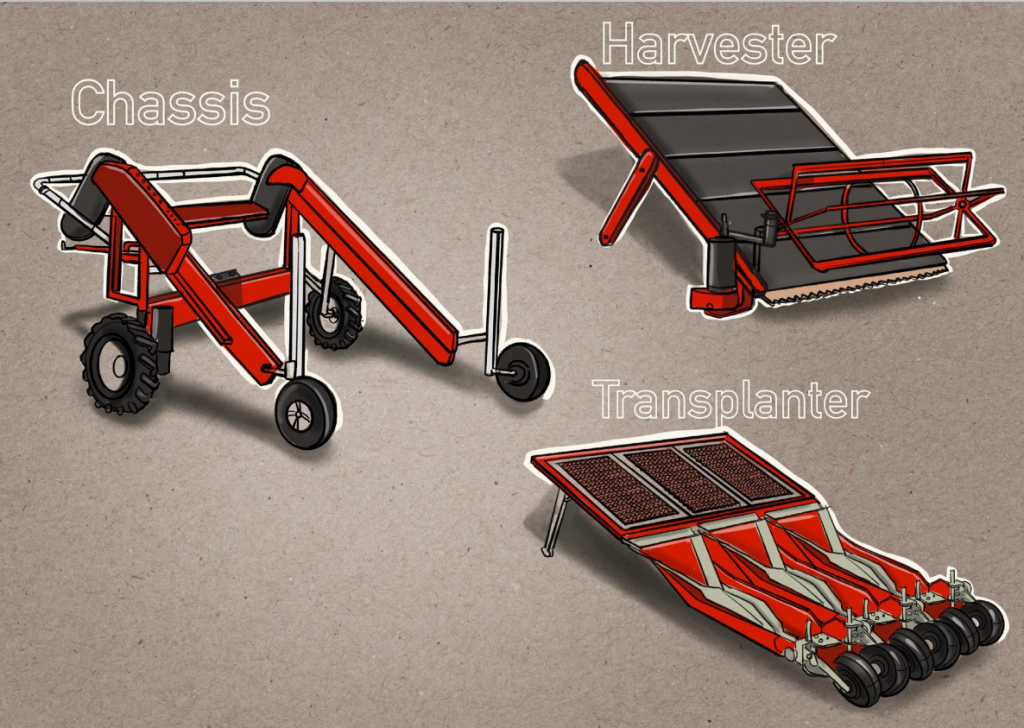
Chassis:
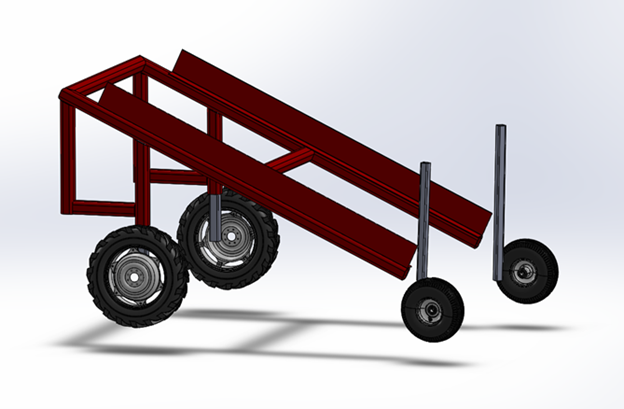
Main part of the design is finished and just needs to be put into CAD.
Still is less of a priority compared to the manufacturing RRP specs, but we are now putting more time into the CAD.
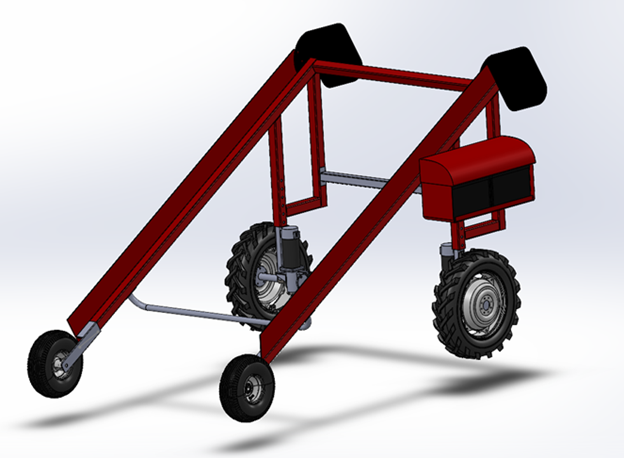
Weight analysis shows us at 165lbs so far.
Model is structurally not complete and still performs well in FEA
Control panel and operating arm not shown and will be placed on the opposite side of chassis.
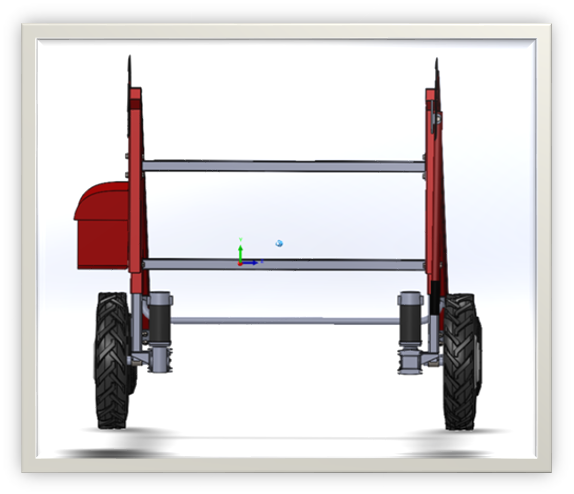
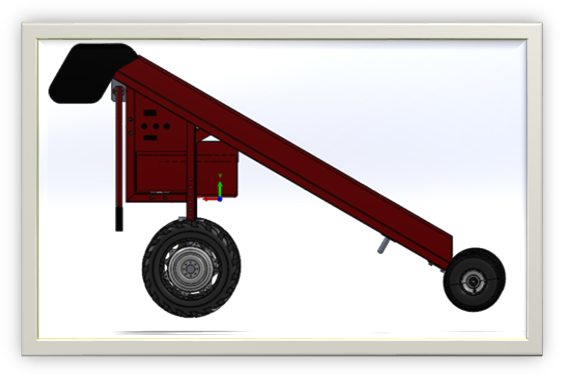
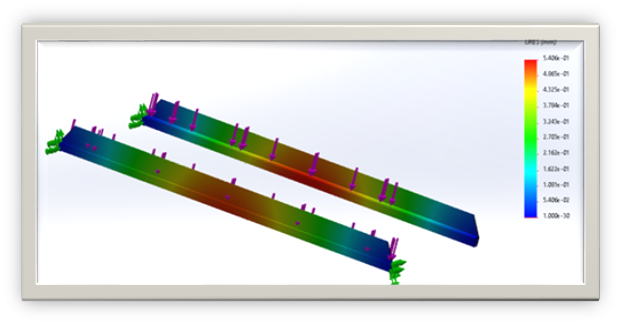
With a 5 times greater static loading the legs only have 0.021” of displacement.
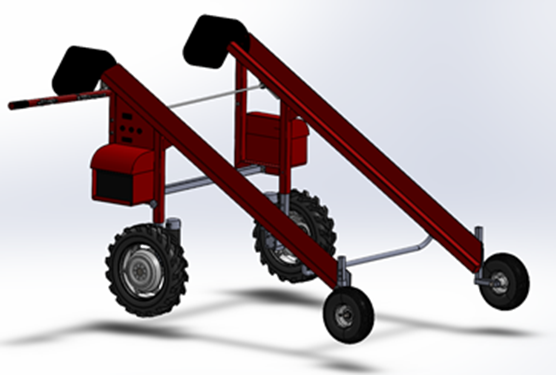
Winter 2021
We developed a new handle idea that will work well.
Front and rear adjustments for wheels redesigned.
Split the batteries and will most likely have to move them forward for balance. The mount for the batteries then would add rigidity to the legs.
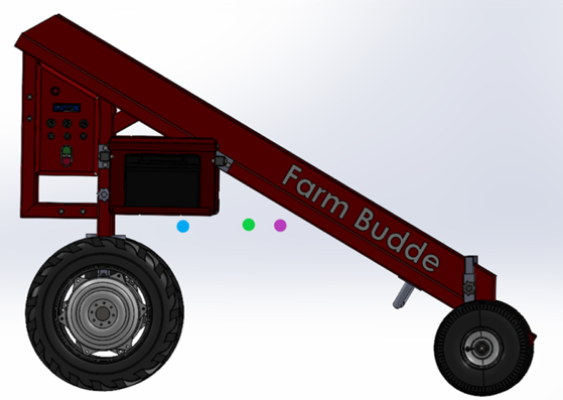
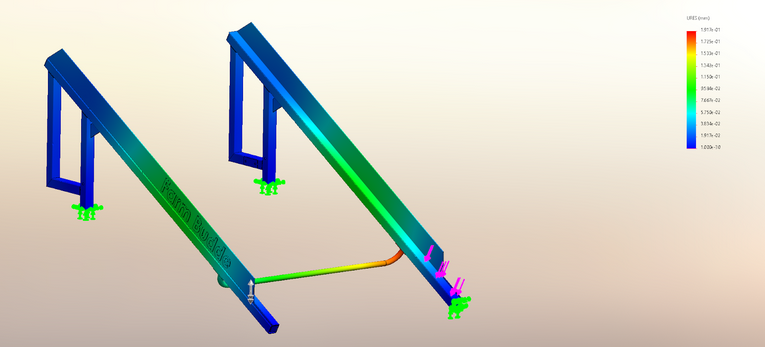
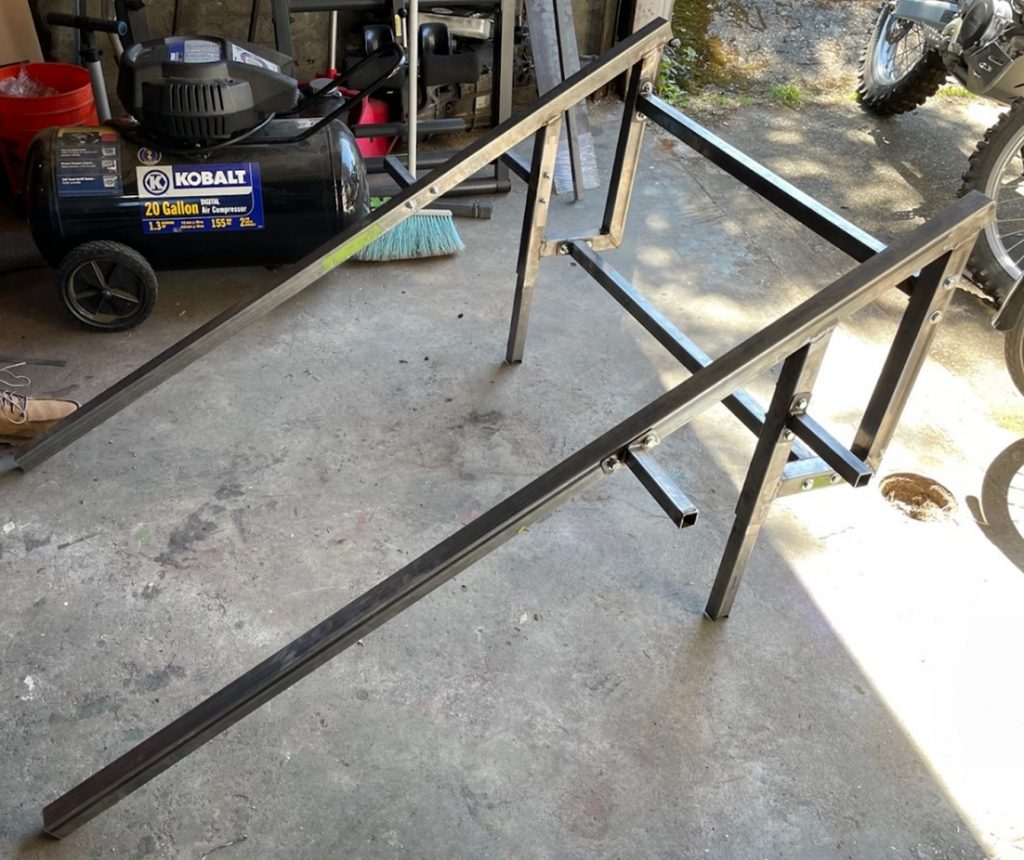
Chassis constructed from mild steel square tubing.
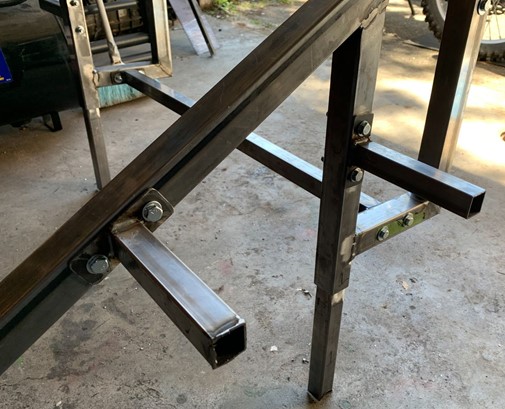
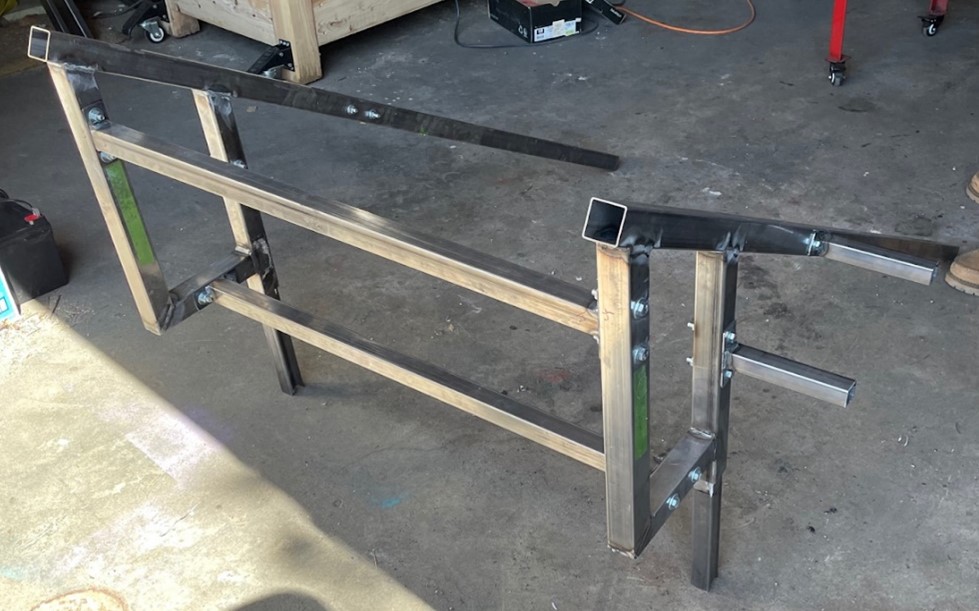
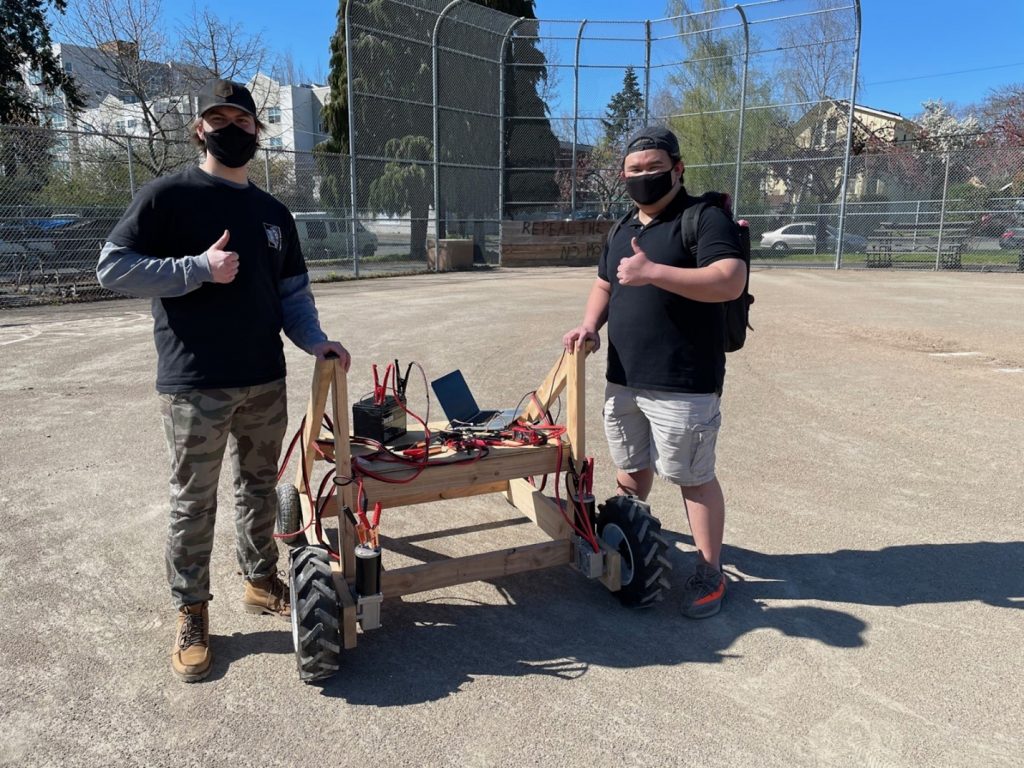
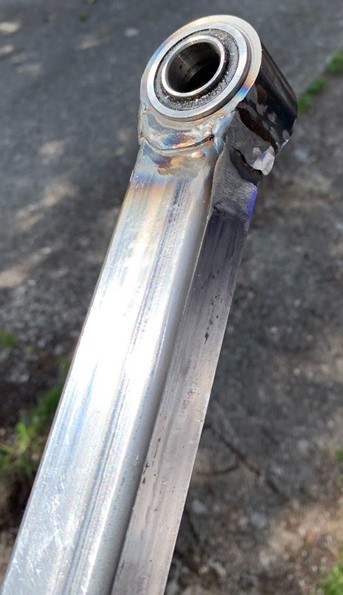

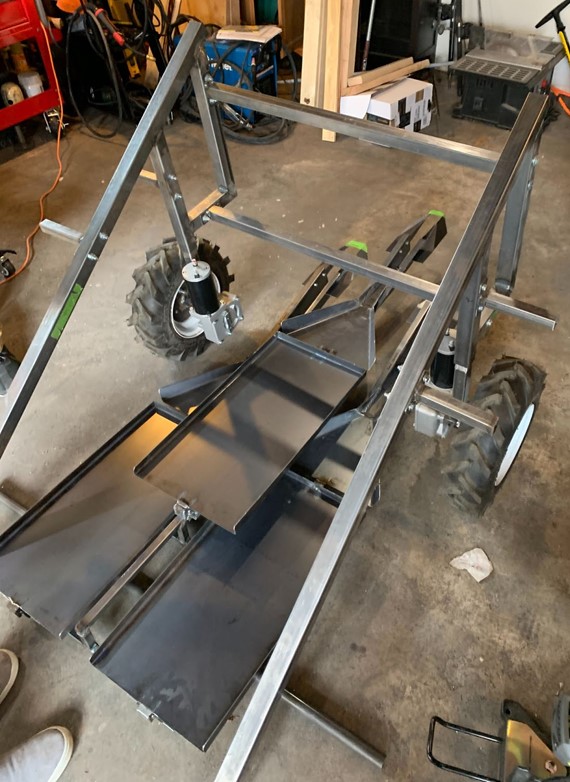
Harvester:
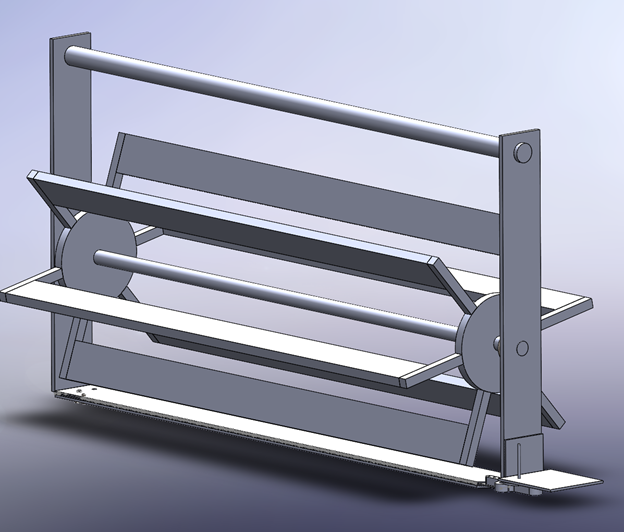
CAD (via SolidWorks) of plant wheel and bandsaw assembly for the Harvester attachment
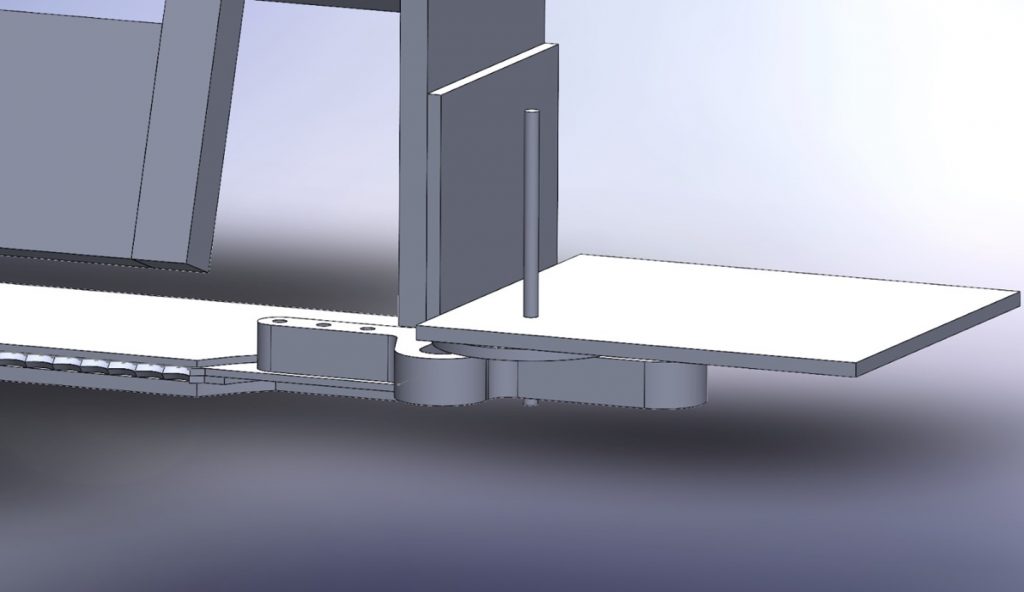
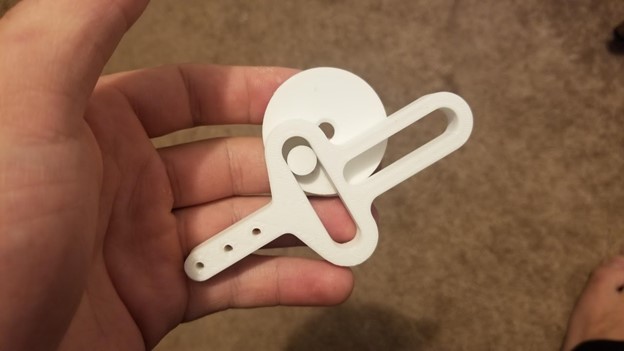

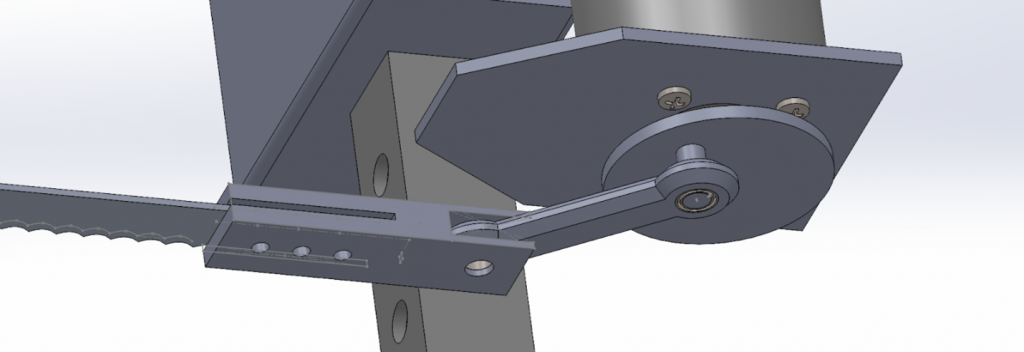
Winter 2021
The Scotch-yoke mechanism is going to be replaced with a crank and slider after further consideration. Upon additional research of the scotch-yoke mechanism, it is evident that applications that use said systems stand vertically rather than flat. Machining of a crank and slider will be much easier
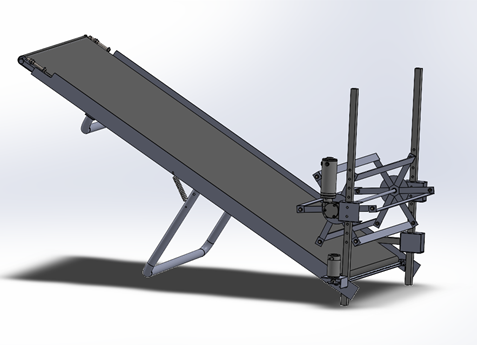
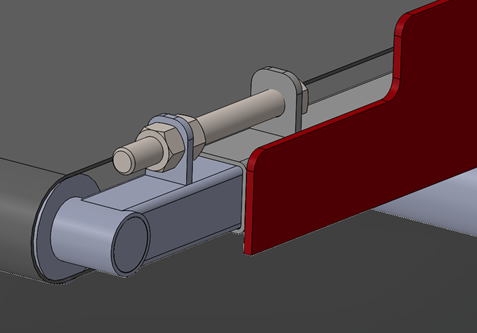
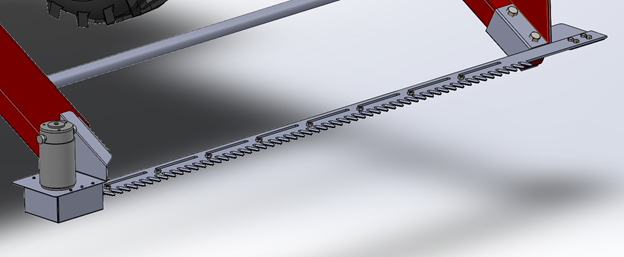
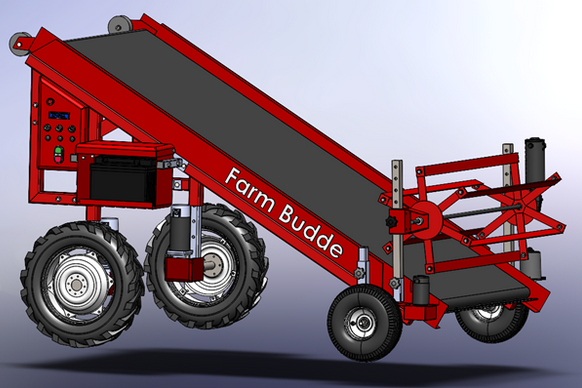
Transplanter:
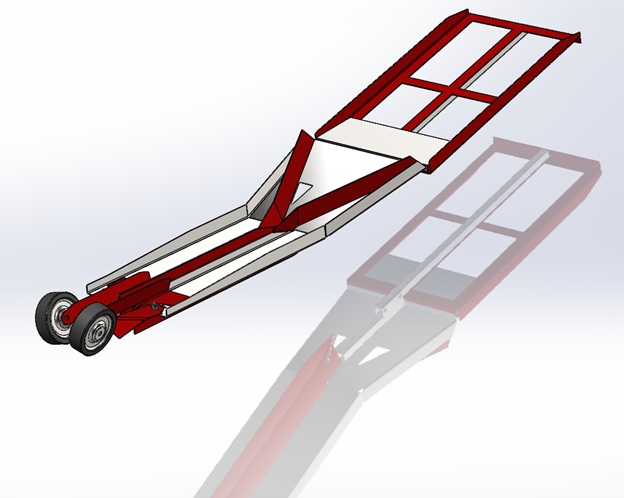
First Transplanter CAD design via SolidWorks.
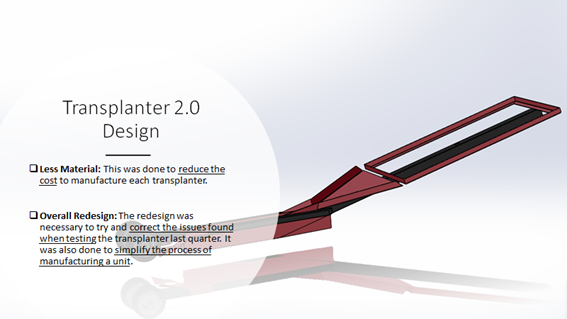
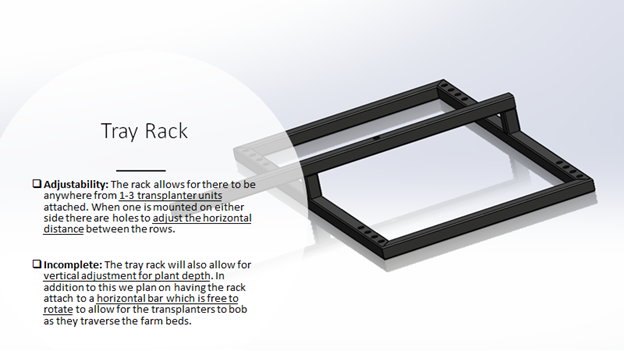
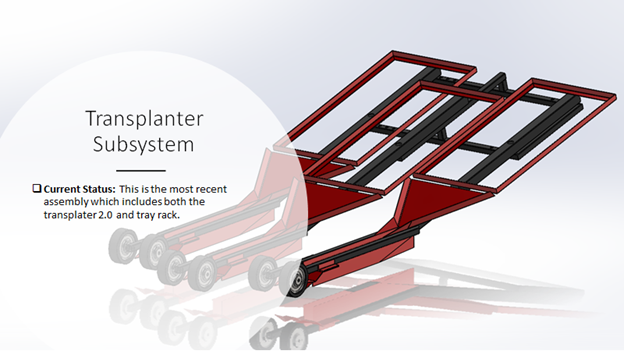
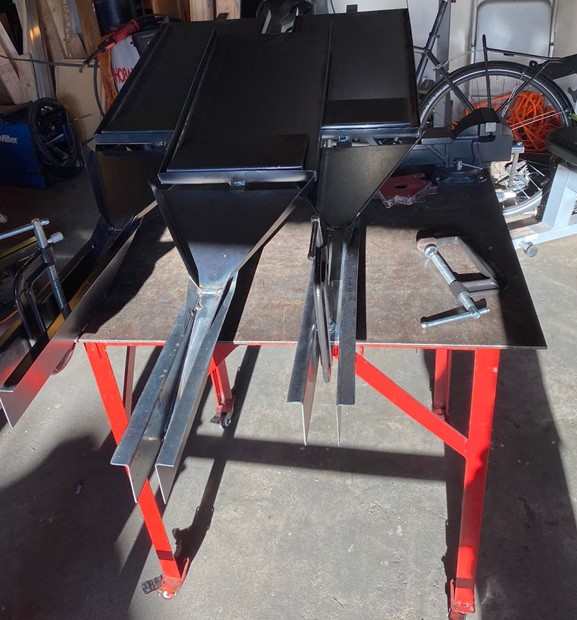
All 3 Transplanters with tray and funnel installed
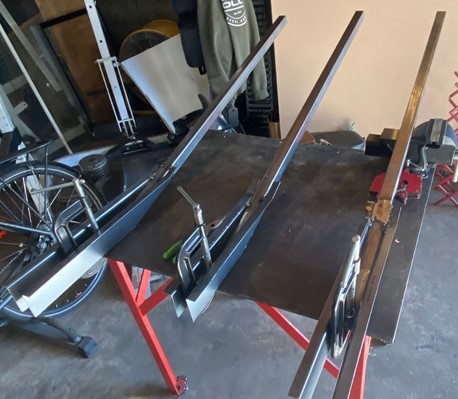
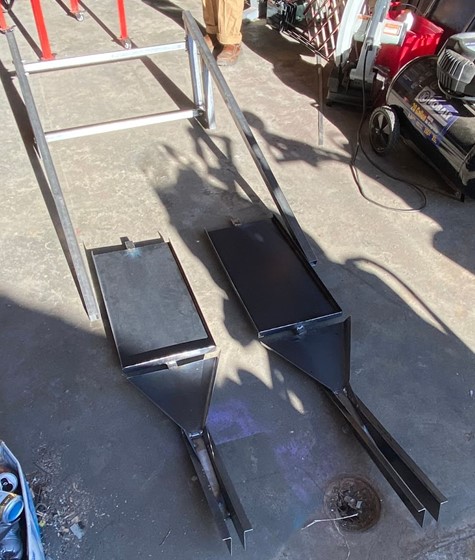
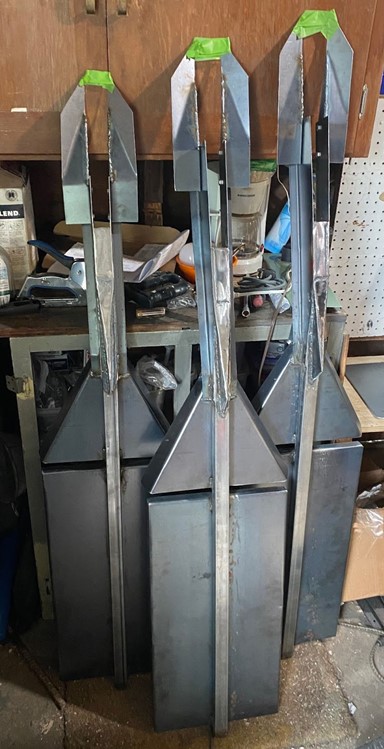
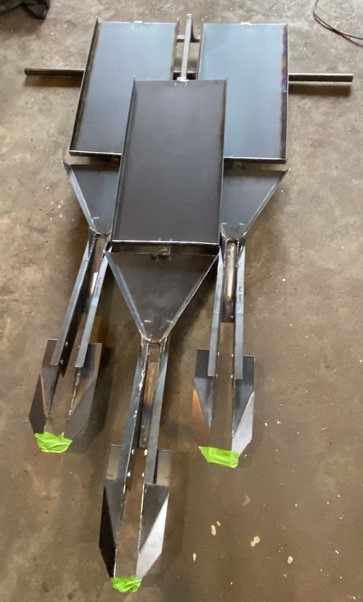
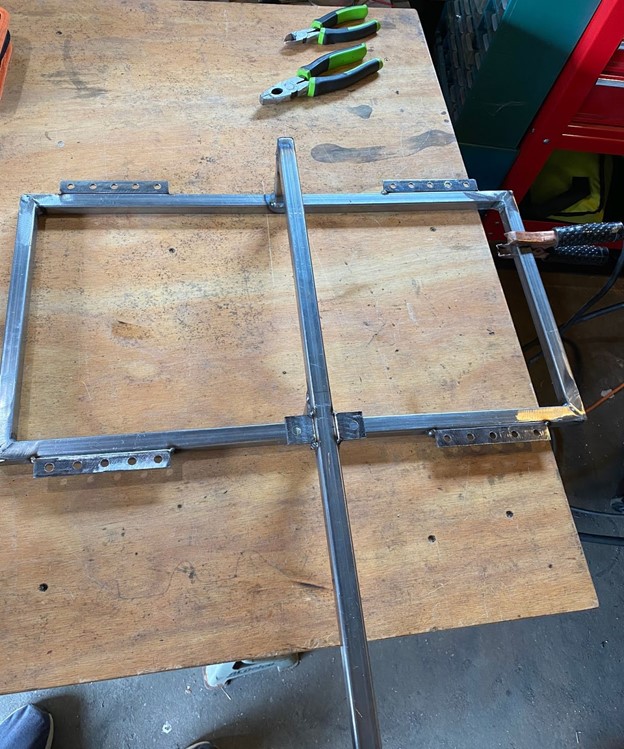