Goal of the Mechanical Team
The Mechanical Team designed ARTEMIS to meet the mechanical criteria outlined in the Design Specifications. The following list defines success for the mechanical subsystems:
- Waterproof Rating
- Aquadrone Stability
- Aquadrone Speed
- Wind Conditions
- Visibility
- Operating Temperature
1) Waterproof Rating
For this specification, we needed to ensure that the electronics housing would be waterproof. Due to the nature of our project, the device needed to be a very high IP rating to ensure the safety of the electronics. This was the most concerning spec for our to meet, and therefore we opted for a C.O.T.S solution that is already rated at the rating we needed, IP68. We went with the PolyCase, a marine electronics box designed specifically to waterproof the insides. We also purchased a cable gland to help ensure the penetration point of the wires is also IP68 rated.
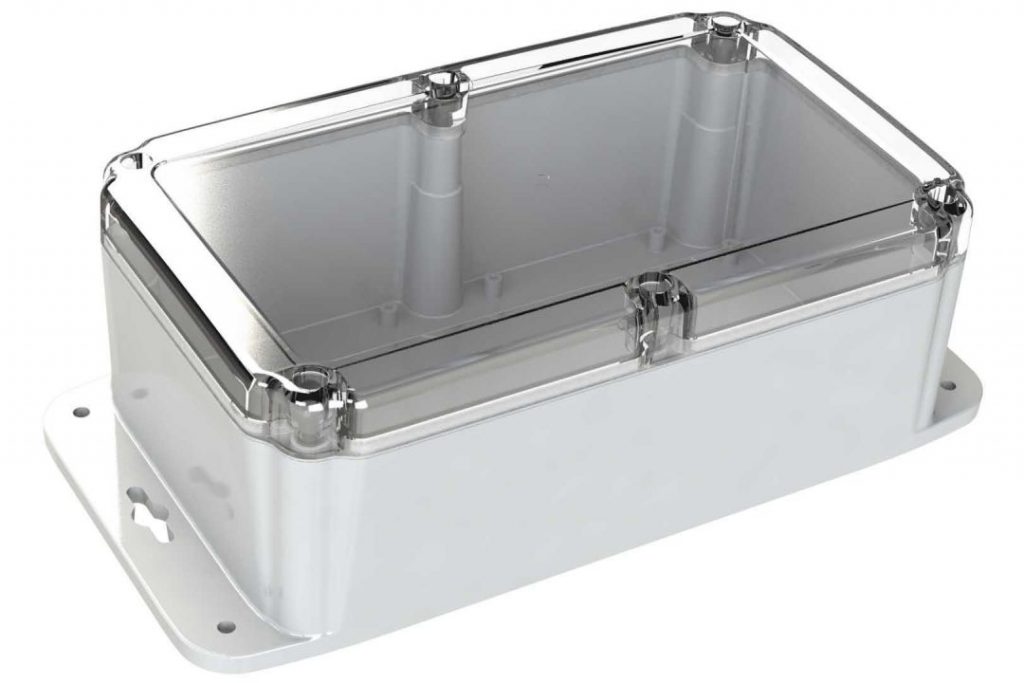
The ML-58F PolyCase containing electronic components.
2) Aquadrone Stability
For this specification, we needed to ensure that the aquadrone would be stable in the water and not tip over with the tides and swells of the body of water. We tested increased angles of 20, 30, 40, 50, and an extreme angle of nearly 80 degrees for the drone to come back to a resting position on the water. All tests passed, proving our pontoon design a success.
3) Aquadrone Speed
For this specification, we wanted the aquadrone to be fast enough to be fun to use, but not too fast to pose as a safety concern. We were aiming for 1knot on the water’s surface.
Furthermore, this was our statistical test, which was a requirement for our senior project. During our testing, we took multiple trials of testing the speed of the aquadrone. We got multiple times for the same distance traveled, as depicted by the ruler on the dock. The testing and images are below:
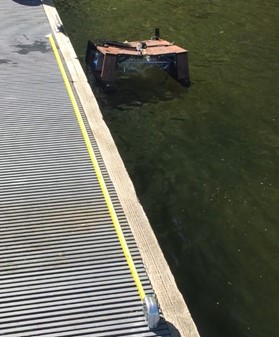
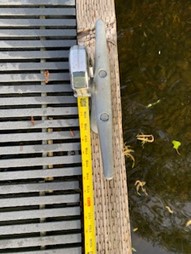
The following data shows the statistical results of the speed tests:
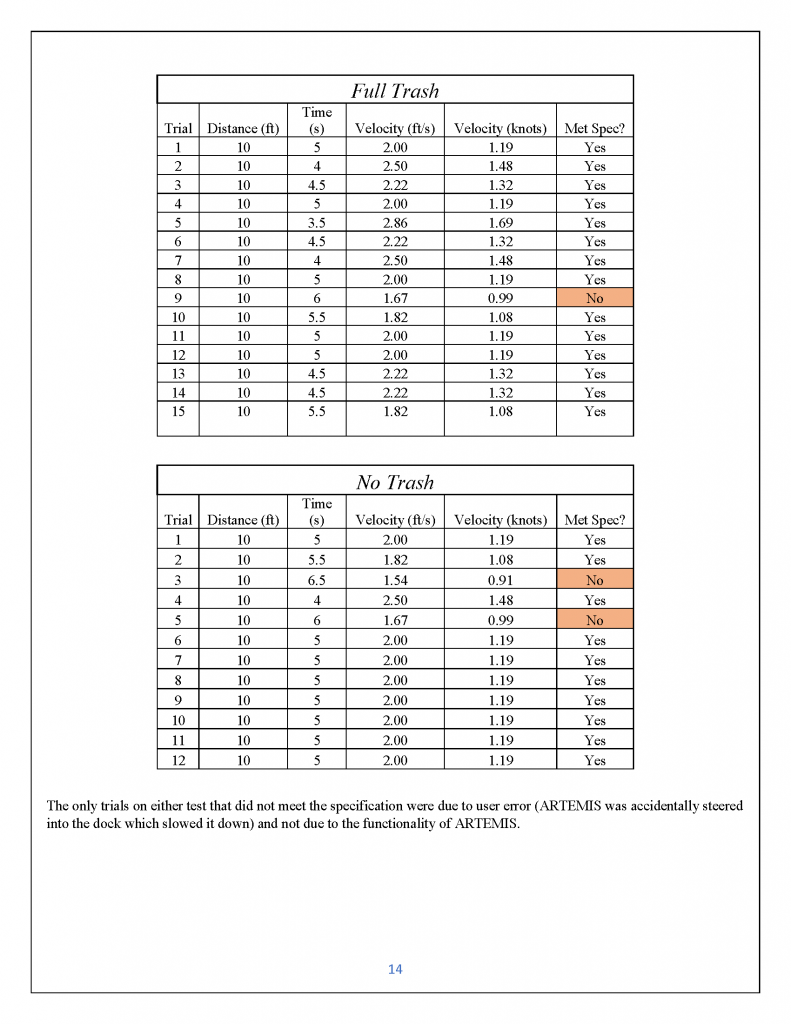
Test Deviations
Due to some of the mishaps from the user, we did more than the 11 trials we identified for each test to make up for those tests where we hit the dock. However, we still wanted to include the data from those trials just to have an honest and full picture of the reality of this test. Also, we only ran the test for a full load of trash and no load of trash because that would give us a best-case and worst-case scenario. We determined that this would be sufficient without testing ARTEMIS with a partial trash load. Additionally, we would like to note that the average speed of ARTEMIS throughout the full trash test was higher than that of the no trash test (Avg. speed (full trash) = 1.27 knots, Avg. speed (no trash) = 1.16 knots). This makes sense because after testing we noticed that the pipes had very slowly taken in some water which made ARTEMIS sit lower in the water, and we completed the no trash test last. The water collected by this point would create more drag and slow ARTEMIS down. Lastly, one factor we did not take into consideration was the direction we were steering ARTEMIS. Since we were at a boat launch and there were boats out on the water, one direction was in line with the wake, and the other direction was going against it. We mention this for full transparency, but the deviations are minor and accounted for by doing the 11 trials for a statistically sound test.
4)Wind Conditions
For this specification, we needed to do an engineering and physics analysis to determine the wind conditions that our device could handle.
Due to the feasability of actually completing an experimental anlaysis of this specificaiton, we chose to do a free-body diagram analysis. Below are the results:
5) Visibility
For this specification, we wanted to ensure that ARTEMIS would be visible from a good distance off shore in case the camera stopped working. For this test, we placed ARTEMIS at set distances on Wallace Field with the high visibility flag. We then timed someone on the reaction time it takes to identify ARTEMIS and the orientation it is facing. Sadly the pictures we took, including this one of Andrew, do not do the true in-person visibility justice. We only took 1 measurement at the full length of the field, and noticed that there wasn’t any significant time difference between the mid-field measurements and likely wouldn’t be any. Therefore, we concluded this test met our visibility specifications.
Here are the timing results:
55 Yards (165 ft Mid-Field)
1.5 seconds
1.71 seconds
1.27 seconds
110 Yards (330 ft Full-Length)
1.3 seconds
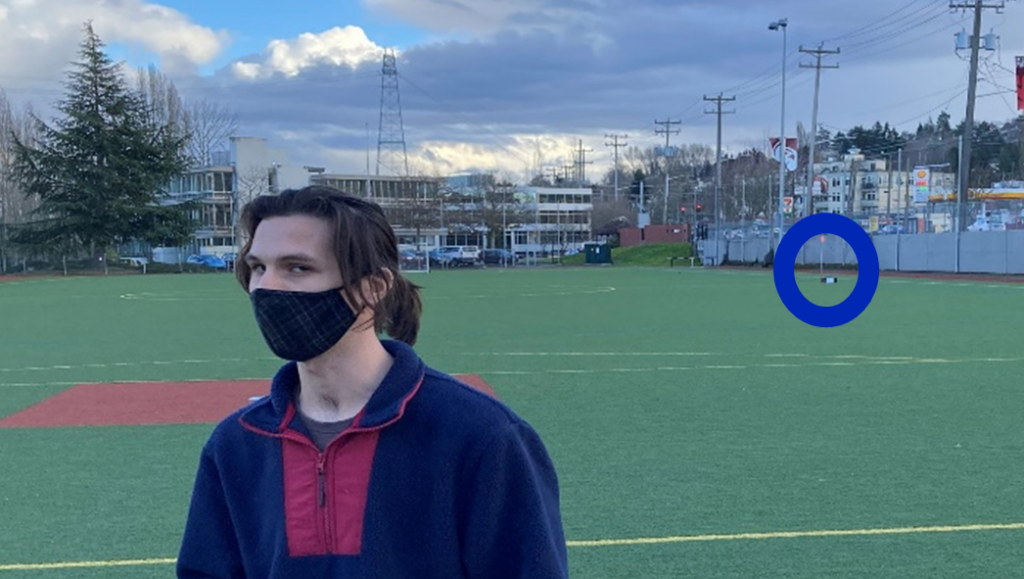
6) Operating Temperature
For this specification, we are ensuring that ARTEMIS can operate successfully in any water environment, considering each of the materials that make up ARTEMIS. All of the materials we have used have been confirmed to work within the operating temperatures we specified, and we can confirm this spec is successful.
Part Description | Operational Temperature |
(3) ¾” x 4in. X 8ft Cedar Hardwood | Anything below 669.2°F |
(2) 20in x 32in x 0.093in Clear Acrylic Sheet | -40°C to 80°C (-40°F to 176°F) |
(4) 3in. L Bracket | Up to 750°F |
8 x 1-5/8 in. Phillips Bugle-Head Construction Screw (1 lb./Pack) | Up to 750°F |
Varathane Gel Wood Stain- Red Mahogany | N/A, 55-90°F for Initial Staining |
Varathane Spar Urethane, Oil-Based | N/A, 55-90°F for Initial Staining |